How to spray inorganic zinc primers
Material handling is the key
It is more about how you handle the material than what pump you use. Mixed primers weigh 20-30 lb/gal. Inorganic zinc is basically powdered zinc metal mixed into a base fluid that has no organic resins to keep it in suspension. This is done because the goal is to apply the zinc in such a way that it is laid down touching all other zinc and the substrate metal.
The great corrosion protection is achieved only if the sacrificial zinc is conductive to the metal substrate. Epoxy or polymer binders significantly prevent that conductivity from happening. That is the difference between the inorganic and the organic zinc coatings.
From a fluid handling standpoint, the material must be fully conditioned into suspension, and then kept in suspension throughout the time it is in the pail, pump, hose, and gun. If it is allowed to settle, or get strained across a ball and seat, it will not matter what equipment you are using - you will have problems.
Getting started / setup
- Do not mix the zinc in until you are ready to spray
- Be ready to spray the entire batch without stopping
- Avoid having the gun too much below or above the pail, as gravity will settle the zinc in the hose
- Use a 3/8" ID hose of a 50' maximum length and a short whip
- Avoid sharp elbows on siphon or outlet fluid lines
- Use a 30-60 mesh max. filtration on the pump or gun
Mixing the fluid and zinc together
- Use a powerful mixer - at least a 3/4 HP drive with a 5" Jiffy-type mixer
- Slowly add the powder and continue mixing for 5 minutes
- Strain the mixed fluid through a 30 mesh screen
- Mix it for another 5 minutes
- Keep the mixed fluid under agitation until you have finished spraying and are ready to flush
Start spraying
- Start with the spray gun off of the hose
- Load and circulate fluid through the hose and back to the supply pail at a low pressure
- Connect the gun and add enough pressure for a pattern
- Spray
When you have stopped spraying
If you have to stop spraying, relieve the fluid pressure on the pump, hose, and gun. When a pump ball is holding pressure across the seat, there will be zinc particles trapped between the ball and the seat. The difference in fluid pressure across the ball and the seat will strain the solvent out, collecting many zinc particles at that point. This causes two faults:
1. Packed out particles plug the passage and restrict ball movement.
2. Some particles keep the ball from fully seating resulting in a high velocity "wire draw" fault on the ball and/or seat.
This applies to any valves in the system, pump checks, any ball valves, and the spray gun. Even for short stoppages, relieving the fluid pressure and/or low pressure circulating goes a long way toward keeping things working well. Flush as soon as you have finished spraying.
Flushing
Flushing tends to wash the zinc out of the suspension even more. Do not let it sit in the pump. Flush out at a fairly high velocity to clean out the dead areas. Remember, velocity cleans, not pressure.
- Circulate the flush back into the pail with the agitator off, and take the siphon pick-up tube up off the bottom
- Finally, dismantle and clean the lower to get any packed zinc off of the checks and packings
Pump lowers
Xtreme lowers vs. the competition
Graco Xtreme lowers are the best to use for these materials, mainly because they are easier to knock down and clean or service than the competitors' pumps. None of the our competitors offer pump lowers with better balls, seats, or rod and cylinder coatings than Graco offers, but also some of those models are much harder to service.
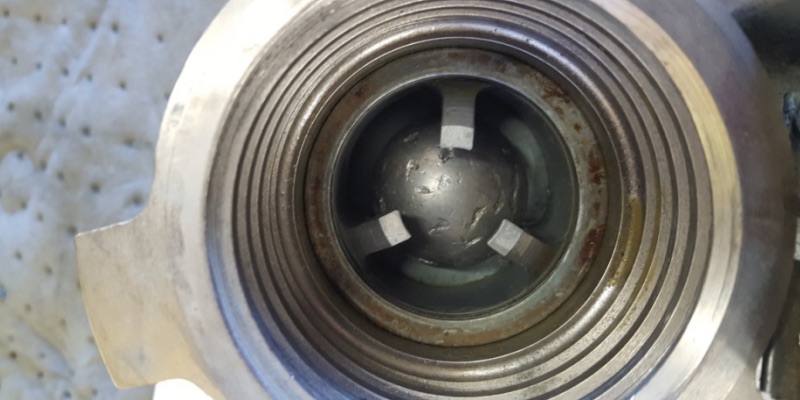
If the balls are the failure point for particular inorganic zincs, we do offer ceramic balls that will hold up somewhat better. The seats are made from carbide and are extremely hard. Seats and balls should always be replaced together. The balls may look much worse, but the smallest wear on the seat will allow some leakage, and will quickly start tearing into a new ball. The image above shows an example of a heavily damaged inlet ball check.
Aluminum oxide ceramic balls
for Graco Xtreme lower pumps
Ball size | Material | Part number | Piston | Inlet valve |
0.312 | ceramic Al2O3 | 119259 | 36-58 cc | |
0.438 | ceramic Al2O3 | xxxxxx | 72 cc | |
0.500 | ceramic Al2O3 | 119260 | ||
0.750 | ceramic Al2O3 | 111453 | 145-180 cc | |
0.875 | ceramic Al2O3 | 118602 | 220-250 cc | |
1.000 | ceramic Al2O3 | 117321 | 290 cc | 36-115 cc |
1.250 | ceramic Al2O3 | 119264 | 145-180 cc | |
1.500 | ceramic Al2O3 | 131271 | 220-290 cc | |