Concrete Surface Preparation Part 1: Unsound Concrete
Explore Graco’s guide to concrete surface preparation and why the removal of an unsound concrete symptom such as delamination is essential for proper bonding.
Blasting Concrete for Proper Bonding
The problem with concrete is that you never know what it will do when you hit it with an abrasive blast.
Fines and cement paste break away easily enough, exposing the harder aggregate. Unlike steel, the compressive strength of concrete is not uniform, meaning that blasting won’t impart a consistent surface profile or anchor pattern. A blasted concrete surface is a cratered landscape of cavernous pores and capillaries.
For proper bonding to occur, repair mortars, concrete overlays and coatings must penetrate and fuse into the substrate’s capillary network. When the network is blocked, blasting opens it up, exposing the aggregate and roughening the landscape.
But with no peaks and valleys to press tape to and measure by depth micrometre, how does the blaster know when he’s achieved the specified surface profile? How is it possible to specify a profile for concrete?
There are other problems. As well as ensuring the concrete surface is prepared correctly and adequately roughened, it must also be sound and contaminant-free. However, due to the relatively porous nature of concrete, contaminants often penetrate deep into the surface, weakening the substrate to a depth beyond the effective reach of abrasive blasting. For other applications, like decorative finishes, only the superficial, friable layer of hardened cement paste should be removed. What do you do when abrasive blasting is overkill or underkill?
This guide to concrete surface preparation walks you through the solutions to these problems and more. But first, let’s understand how and why concrete can fail, and how it can be made sound again.
Sound Concrete
When a coating, overlay or repair mortar is applied to unsound concrete, the bond between the two materials may hold but, when pressured, unsound concrete will simply detach from the slab. Cracks, microcracks, blisters, scaling, spalling, or delamination are symptoms of unsound concrete that must be removed and then patched before surface preparation can proceed.
Contact an Expert
6 Symptoms of Unsound Concrete
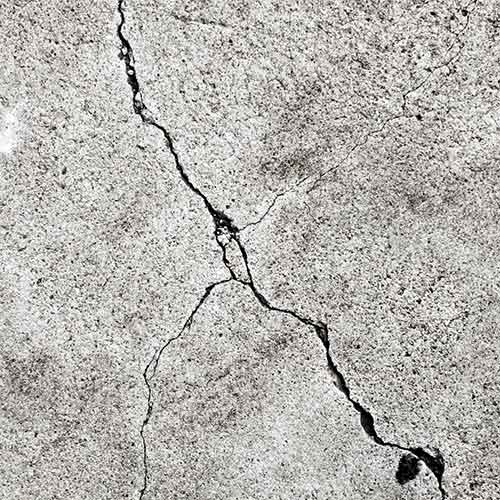
Visible cracks are the most obvious symptom of unsound concrete, and there are several causes for this. Superficial cracks are caused by rapid surface water loss during the curing process. Settling of the subgrade can crack the slab in two. Heavy loads or impacts can cause visible cracks immediately, or cause microcracks which later propagate into visible cracks.
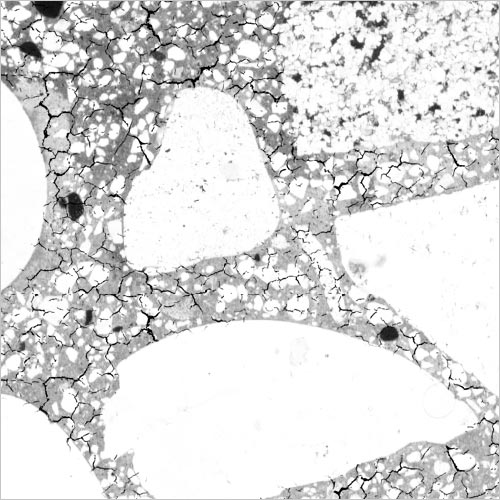
Microcracks are invisible to the naked eye, measured on the scale of microns. Microcracks are caused by overloading, impacts from dropped loads and impact tools such as jackhammers and scabblers, freezing and thawing, and temperature differentials that occur during cement hydration. Bruising occurs when microcracks create a network near the surface. The unsound concrete then crumbles away, exposing aggregate.
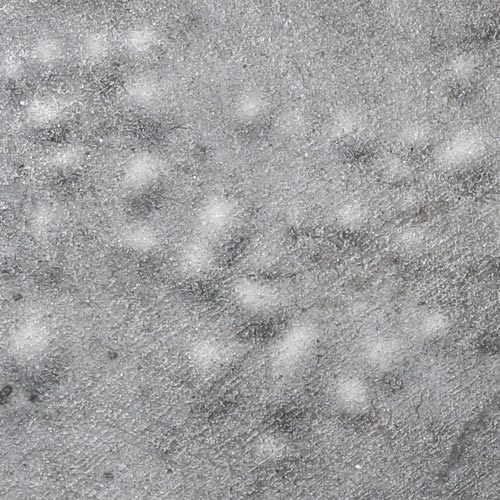
Blisters form when air bubbles are trapped under the surface, unable to escape due to the surface drying prematurely due to wind, an overly-sticky mixture that seals the surface too quickly, or premature finish applied to the concrete, by trowel, for instance.
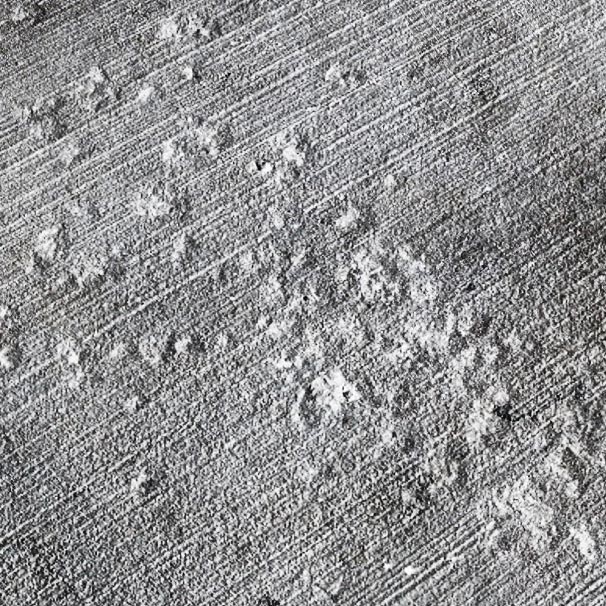
Scaling is caused when water freezes in the pores and capillaries in concrete. When the hydraulic pressure of the expanding ice exceeds the tensile strength of the concrete, scales of mortar detach from the surface, exposing aggregate.
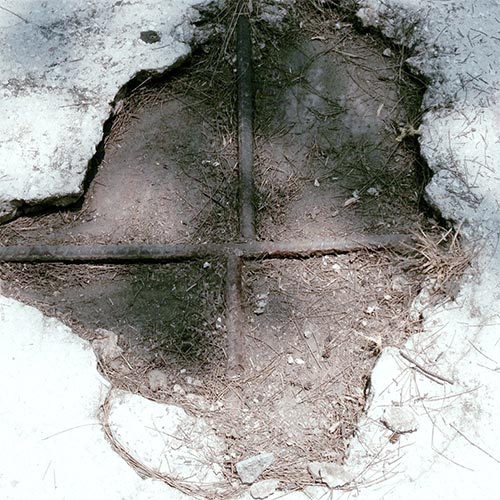
Spalling is similar to scaling, except the expansion occurs from deeper within the concrete, causing the surface to disintegrate into larger fragments. Common causes are rebar corrosion due to carbonation, intense heat that causes water vapour to expand violently, improperly constructed joints, and crack deterioration.
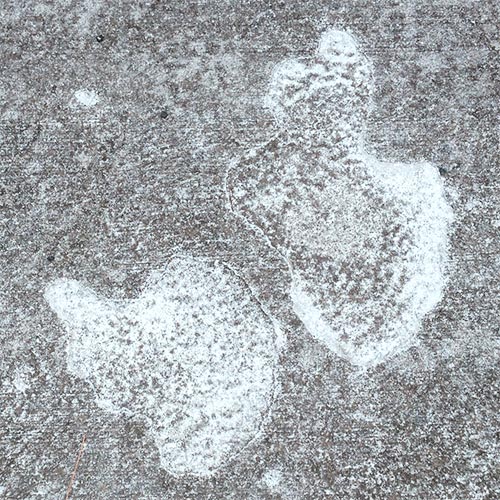
A delamination is a hollow, horizontal plane below the surface that forms when a finish is applied before water and air can bleed out of the concrete. When crushed by traffic or a heavy load, the delaminated section detaches from the slab, exposing aggregate.
6 Causes of Unsound Concrete
Carbonation
Carbonation develops when carbon dioxide penetrates the surface through pores and microcracks, and reacts with moisture and calcium hydroxide in the cement, forming calcium carbonate. This starts by hardening the concrete, but it also reduces the pH level from 13 to 8. This reduction in alkalinity leaves embedded steel rebar susceptible to corrosion.
Rebar Corrosion
Rust is a hydrated iron, and is more massive than the steel it replaces. The increasing rust mass creates tensile stress, causing concrete to crack and spall.
Chemical Attack
Sulphates seep into concrete through the groundwater, react with hydrated compounds and expand, causing mechanical failure. Chemicals can also soften, erode and dissolve cement paste.
Fire Damage
Concrete won’t burn; however, high heat causes the concrete to lose the majority of its compressive strength, flexural strength, and elasticity. Expanding water vapour trying to escape can cause spalling.
Overloading/Impacts
Placing concrete under a heavy load, especially by impact, causes microcracking and cracking. Impact tools can cause extensive microcracking.
Over-wet Concrete
Too much water in the mix leaches cement to the surface. The surface will dry before setting occurs, causing shrinkage, cracks, reduced compressive strength, and laitance.
How to Detect Unsound Concrete
Visually inspecting the surface will expose the worst of the damage; the cracks, spalling, scaling and crushed delamination; however, the full extent of the unsound concrete is not always apparent.
Perhaps the easiest thing to do is to tap around visibly weak areas with a hammer. If the head of the hammer bounces, the concrete’s compressive strength is good. If the hammer indents and pulverizes the surface, the concrete is unsound and should come out.
Dragging a screwdriver across the surface can also expose unsound concrete. If it leaves a shiny white streak, the concrete is sound. If it scratches off powder, the concrete is unsound.
Cases where pockets of air, water or unwetted material have formed under the surface are not so easy to detect; the surface may be sound enough to pass the hammer or screwdriver test, but structurally compromised. Listening to the sound made when tapping the concrete reveals areas of differential density. On large surfaces, these hollows can be detected by dragging a chain over the surface, or by using equipment that flogs the surface with an array of chains.
Once the extents of unsound concrete have been outlined, removal can begin.
Removing Unsound Concrete
When the majority of the concrete surface has been compromised, it’s best to remove the affected layer by mechanical means, discussed below. When spot-removal of compromised sections is called for, a common method is to chip away the unsound concrete with a hammer, jackhammer, concrete breaker or other impact tool.
The best practice is to start at the centre of the weakened area and proceed to the edge. However, feathered edges should be avoided, even if you are patching the void with a self-levelling compound or epoxy that can be spread thin. At some point, the coating application will be too thin to cover the profiled surface adequately. Chipping deep, acute edges provides better tensile bond strength, but a perpendicular or undercut edge is best.
When filling a void with concrete or other thick compound, the best practice is to saw cut edges at right angles around the compromised area. While chipping outwards towards the edge, the surface material inside the cut will break away, leaving a perpendicular edge.
Repairing Unsound Concrete
Once the unsound concrete has been removed, the voids can be filled with concrete, mortar, grout, plaster, putty, epoxy or another patching compound. In addition, concrete has naturally-occurring voids that should be filled to shore up structural integrity.
The role of abrasive blasting in concrete removal
During the concrete removal stage, there are two opportunities for abrasive blasters to ply their trade.
Saw cuts leave smooth vertical surfaces with dust-filled pores. Blasting opens the pores and roughens the surface, providing an interface for the patching material.
Impact tools used to remove unsound concrete but cause extensive microcracking. Patching a surface weakened by microcracking defeats the purpose of the repair. Abrasive blasting is the preferred method to remove the microcracked surfaces.
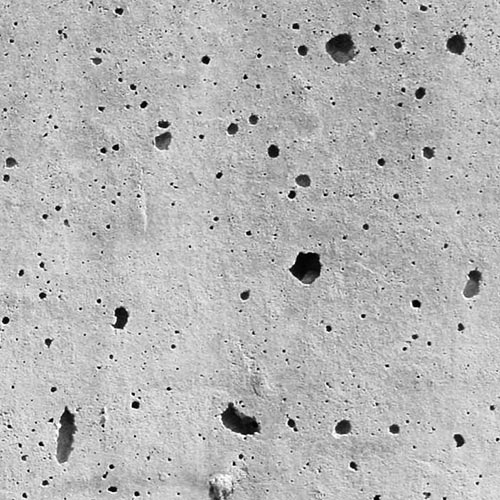
Bugholes are voids which develop next to a formed surface caused by bubbles of air and water that migrate to the forms to escape the heat produced by cement hydration.
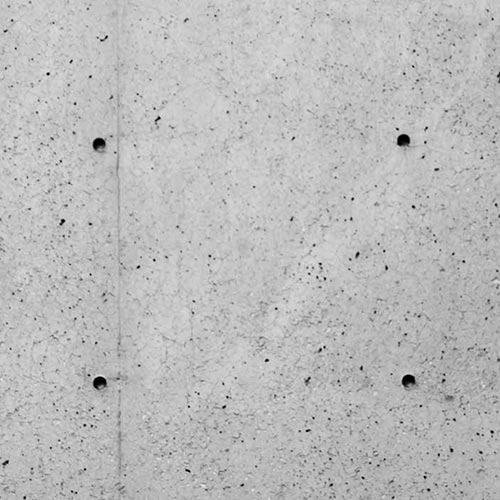
Tie rod holes are voids that pass through the concrete, caused by the removal of the tie rods that held the forms together as the concrete cured. Tie rod holes and bugholes should be filled before proceeding.
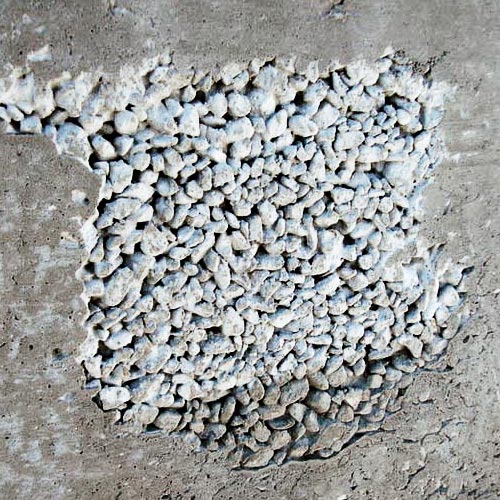
A honeycomb is a cluster of coarse aggregates where mortar did not penetrate. The aggregates are tightly packed but unbound, with poor compressive strength and negligible tensile strength. The aggregates need to be removed with power tools down to bare concrete, then filled.
Voids are not the only surface defects which require fixing. Projections that extend past the dry film thickness of a coating can cause the coating to fail, especially around sharp edges. When the overlay is a self-levelling compound, it may require an excessive amount of material to cover projections adequately. Mortar splatter, fins, ridges and other protrusions exceeding 1/16th inch should be ground down or chipped away.
Before patching with a cementitious product, the substrate should be in a saturated surface dry (SSD) condition. This entails spraying it with a hose then wiping it off so that the pores are saturated, but no free water remains on the surface.
If the surface is wet, the water-to-cement ratio will rise along the bond interface, resulting in shrinkage, microcracks and weakening the bond. When the surface is unsaturated, it will pull water from the repair material, potentially resulting in insufficient cement hydration and reduced strength along the bond.
Once the sound concrete surface is restored, the next step is to remove contaminants from the concrete. In Part Two of our series on Concrete Surface Preparation, we’ll look at the different forms of concrete surface contaminants, their causes, and how they can be removed (hint: abrasive blasting isn’t always the answer).
The Role of Abrasive Blasting in Concrete Patching
Depending on the required roughness of the application, patched areas may need surface profiling by abrasive blasting.