Motoren van landbouwvoertuigen verven
Graco-apparatuur speelt een sleutelrol in een nieuwe automatische motorcoatinglijn in de fabriek van de MANTA Group in Italië.
De MANTA Group, gevestigd in Foggia, Italië, richt zich al meer dan 30 jaar op de assemblage en coating van onderdelen voor de lucht- en ruimtevaart en de auto-industrie. In 2021 kreeg het bedrijf de opdracht om motoren voor landbouwmachines te verven. Om deze taak uit te voeren zocht MANTA naar een pool van leveranciers om een volledig digitale, Industry 4.0-conforme, geautomatiseerde, flexibele en snelle verflijn te bouwen.
De doelstellingen voor de nieuwe coatinglijn waren uitdagend. Met deze zouden namelijk meer dan 700 motorvarianten in vier verschillende kleuren geverfd moeten kunnen worden, met een capaciteit van 85.000 motoren per jaar. Ook moest deze lijn volledig digitaal worden geïntegreerd met het managementsysteem van het bedrijf, zodat elke coatingstap nauwkeurig kon worden bewaakt en aan de kwaliteitseisen kon worden voldaan.
Gaiotto, Savim en CM Automazione waren betrokken bij de technische aspecten van de fabriek en Graco was verantwoordelijk voor het aanbrengen van de verf. Het verfsysteem met één laag op waterbasis voor de motoren werd voor de start van de productie gevalideerd door een extern laboratorium (CRF).
Soepele samenwerking
De verffabriek is gebouwd door Savim (Arbizzano, Verona, Italië), is uitgerust met Gaiotto-robots en integreert een XD45/59 stapsgewijze transportband die is ontworpen en geleverd door CM Automazione (Giussano, Monza e Brianza, Italië). De lijn biedt plaats aan 116 eenheden met elk een maximale laadcapaciteit van 850 kg. Op volle capaciteit kan de lijn 370 motoren per dag verven.
Voor de verftoevoer, verfaanbrengapparatuur en het kleurwisselsysteem vertrouwde MANTA op Graco en zijn integrator Comaind (San Giovanni Lupatoto, Verona, Italië). Hun samenwerking was van fundamenteel belang in een van de meest kritieke fasen van dit project.
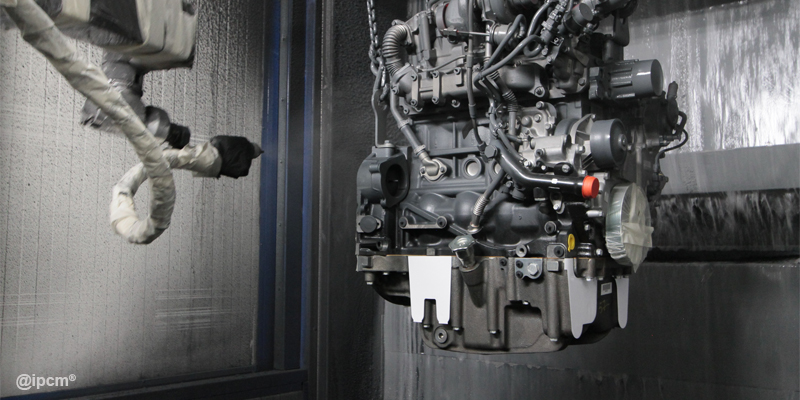
Een gestroomlijnd proces
Elke motor doorloopt een aantal voorbereidingsfasen: afplakken, chemische voorbehandeling met fosforontvetting, reiniging met gedemineraliseerd water en drogen in drie stappen (voordroogtunnel, uitblazen door robot, een oven op 90°C) voordat de motoren door een koelruimte gaan.
De vloeibare verf wordt dan aangebracht in twee watergordijncabines onder druk, met temperatuur- en vochtigheidsregeling, geleverd door Savim, elk met een Gaiotto gelede robot die 180° draait en één kant van de motor verft. De minimale aangebrachte dikte is 50 micron. Een derde handmatige cabine wordt gebruikt voor herstellingen. De lijn eindigt met een droogtunnel en een oven die plaats biedt aan 50 motoren op 100°C gedurende 90 minuten. De motoren gaan dan naar een geïntegreerde kwaliteitspoort voor de uiteindelijke goedkeuring.
Het verfaanbrengsysteem
“We hebben samen met Gaiotto het verftoevoer- en verfaanbrengsysteem ontworpen voor de vier kleuren die MANTA aanbrengt”, legt Davide Galvani van Comaind uit. “De meest gebruikte is grijs, dat goed is voor bijna 90% van de productie. De andere drie kleuren zijn geel, Perkins-grijs en transparant, die gebruikt worden voor de resterende 10% van de volumes.”
De coatingen worden niet per batch gepland; dit gebeurt per motor. Dit betekende dat er een zeer snel kleurwisselsysteem ontworpen moest worden van slechts 30 seconden. De verfbeheereenheid is uitgerust met een container van 1000 kg voor de grijze kleur en vaten van 200 liter voor de andere tinten. De verf wordt geroerd met een ATEX-gecertificeerd elektrisch roerwerk met expandeerbare schoepen en een bijvulsysteem dat is gekoppeld aan een tank van 100 liter waar een Graco Endura-Flo-pomp de verf laat circuleren bij een druk van 2,5-3 bar. Deze tank voedt vooraf het Graco PD1K-meercomponentendoseerapparaat dat is uitgerust met vier afzonderlijke pompen, één voor elke kleur, om een maximale kleurwisselsnelheid op de robot te garanderen.
Bovendien wordt het gerecirculeerde product gefilterd met 60 mesh. Het PD1K-apparaat heeft ook een eigen filtratie-eenheid bij de uitlaat van het pistool. De twee coatingrobots zijn elk uitgerust met twee automatische Graco AirPro-pistolen die voldoen aan de technologie. Het ene pistool gebruikt de grijze verf, terwijl het andere wordt gevoed door kleurwisselventielen die op ongeveer 40-50 cm van het pistool zijn geplaatst, bijna op de pols van de robot; één ventiel dient om het circuit door te spoelen en de andere drie voor de kleuren. De verfbeheereenheid voedt ook vooraf de herstelcabine waar voor elke kleur een pistool beschikbaar is dat wordt geactiveerd met de juiste kleur, afhankelijk van de binnenkomende motor.
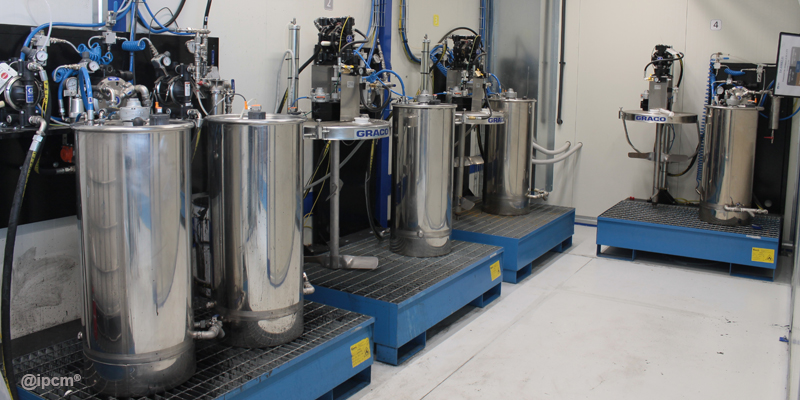
Graco's PD1K in het hart van het systeem
“We hebben gekozen voor het Graco PD1K-meercomponentendoseerapparaat omdat hiermee de verfstroom direct bij het pistool kan worden geregeld en kan worden aangepast aan de beweging van de robot tijdens het verven”, voegt Galvani toe. “Met deze machine kunnen ook de technische/productieparameters worden geanalyseerd en deze is gekoppeld aan het 4.0-systeem van de lijn.”
Dankzij de unieke op pulsgever gebaseerde zuigeraandrijvingstechnologie en actieve regelventielen biedt de PD1K een nauwkeurigheid van de mengverhouding binnen 1%, waardoor elke keer weer een soepele en precieze dosering wordt gegarandeerd. De PD1K behoudt deze uitzonderlijke nauwkeurigheid ongeacht de hoofddruk, de hoogte, de viscositeit van het materiaal, de temperatuur of het gebruik van de pistooltrekker.
Bovendien wordt de spoelzone verkleind door het mengpunt dichter bij het pistool te plaatsen. Dit betekent minder materiaalverlies, sneller spoelen en meer efficiëntie. Volledige spoeling kan worden geprogrammeerd in de geavanceerde weergavemodule van de unit, met de optie om vooraf tot vijf verschillende spoelrecepten in te stellen met individuele oplosmiddelen, tijdschema's en andere factoren.
Ook interessant voor MANTA is de kosteneffectiviteit van de PD1K, dankzij de onberispelijke debietbesturing, snelle kleurwissels en efficiënte dosering. De unieke spoelmethode vermindert het gebruik van oplosmiddelen en materiaalafval met wel 80% en de onderhoudskosten zijn aanzienlijk lager vergeleken met tandwielpompen, waardoor het een budgetvriendelijke optie is voor de MANTA-verflijn.
Het apparaat is uiterst geschikt voor handmatige of automatische toepassingen. Met het apparaat kunnen tot vier pompen bediend worden, verschillende chemicaliën gedoseerd worden en kan de verwerkingstijd voor maximaal drie spuitpistolen bijgehouden worden, op slechts een systeem. Er kunnen tot 30 kleuren worden beheerd in 1K- tot 4K-opstellingen en het is mogelijk om typisch gescheiden materialen te combineren, zoals epoxy en urethaan of verf of water- en oplosmiddelbasis.
Draaiende op hoge kwaliteit
De lijn ging eind 2022 in de volle productiemodus. De opstartfase was een leerproces, vooral omdat verf op waterbasis veel vloeibaarder is dan het equivalent op basis van oplosmiddelen. Aanvankelijk moest er wat handmatig worden aangepast omdat de verfprogramma's van de robots niet volledig waren geoptimaliseerd. Toen de robots werden aangepast, was er geleidelijk steeds minder handmatig werk nodig.
MANTA en hun klanten zijn onder de indruk van de hoge kwaliteit van het lakwerk op de motoren, mede dankzij de kwaliteit en technologische inhoud van Graco's systemen.
Het grotere plaatje van deze motorverflijn
De nieuwe verffabriek en de volledig geautomatiseerde verflijn voor motoren zijn ontstaan doordat experts de handen ineen hebben geslagen. Hier wordt de expertise van Gaiotto, Savim, CM Automazione, Comaind en Graco gecombineerd.
De lijn bestaat uit verschillende stations. Ons verftoevoer- en aanbrengsysteem is er daar één van. Laten we eens een blik werpen op het grotere plaatje. Elk getal verwijst naar een apart station.
- Het afplakstation. Om gevoelige oppervlakken te beschermen tegen binnendringend water tijdens de voorbehandeling
- Chemische voorbehandeling in 3 fasen met fosfidesmering, reiniging met gedemineraliseerd water.
- Voordroogtunnel. De eerste stap van het droogproces.
- Uitblazen door robot. Om eventueel achtergebleven reinigingswater uit de gaten te verwijderen.
- Oven op 90 °C. De derde en laatste stap van het droogproces.
- Koelzone.
- Afplakfase 2. Er worden ongeveer 100 afplakmiddelen aangebracht.
De cyclus gaat verder met het aanbrengen van de vloeibare verf in twee onder druk staande watergordijncabines met temperatuur- en vochtigheidsregeling. De minimale aangebrachte dikte is 50 micron.
Een derde handmatige cabine wordt gebruikt voor herstellingen.
De verflijn voor de motoren eindigt met een droogtunnel en een oven die plaats biedt aan 50 motoren op 100 °C gedurende 1 uur en 30 minuten.
Vul onderstaand formulier in voor meer informatie over Graco's PD1K-systeem.
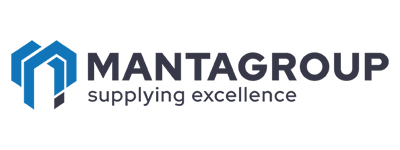
Gerelateerde artikelen
John Deere-fabriek in Mannheim installeert Graco 2KS-verftoevoersysteem
Om aan strikte kwaliteitsnormen te voldoen en de procesbetrouwbaarheid te verhogen, heeft de John Deere-fabriek in Mannheim geïnvesteerd in een nieuw verftoevoersysteem van Graco.
Handmatige processen behoren tot het verleden: automatisering voor een hogere productiviteit
Ontdek hoe goed de Graco AirPro-spuitpistolen met uw automatiseringsproces werken.
Optimaal gecoate tandwielkasten voor zelfaangedreven machines
ProMix Easy- en ProMix 2KS-doseerapparaten en G40- en AirPro-spuitpistolen van Graco bewijzen hun waarde in de productiefabriek voor tandwielkasten van Bonfiglioli in Forli (Italië)