7 significant advantages of automatic lubrication
Lubrication reduces friction and allows moving machine parts to slide smoothly past each other. An automatic lubrication system has many advantages compared to manual lubrication. Find out how it results in extended equipment life, reduced wear and smaller maintenance bills.
Lubrication is a crucial element in the efficiency and life-expectancy of any rotating equipment. According to a study by SKF, over 50% of bearing failures are the result of improper lubrication. Selecting the appropriate lubrication solution can help reduce premature bearing failures and increase machine uptime, productivity and energy efficiency.
What is lubrication?
Lubrication can be defined as the application of oily or greasy substances, also called ‘lubricants’, in order to reduce friction and allow moving machine parts to slide smoothly past each other.
Lubricants form a film between the metal surfaces of machine parts to avoid metal-to-metal contact and to keep the machine running efficiently.
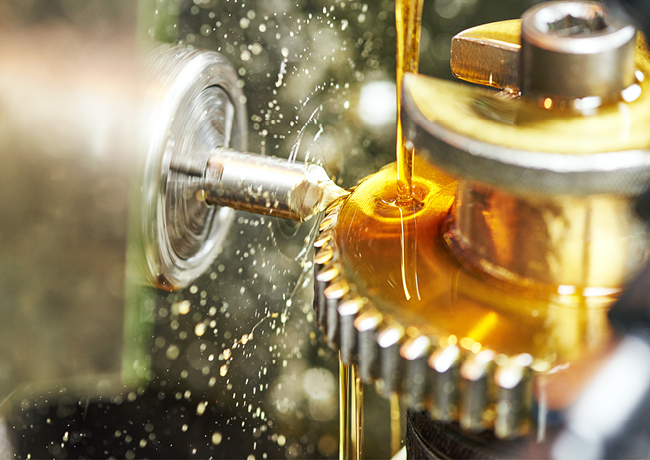
The main functions of a lubricant are:
- Reducing friction by creating a film between two surfaces
- Preventing machine wear
- Corrosion protection
- Cooling by dissipating heat from surfaces
- Sealing
- Cleaning by transporting contaminating particles to filters
Different types of lubrication (manual vs. automatic lubrication)
Lubrication can be performed manually or automatically.
- Manual lubrication
Manual lubrication calls for the intervention of a technician with a grease gun or similar traditional lubrication tool. This lubrication method provides quite a few shortcomings such as increased machine downtime, high maintenance costs and inconsistent lubrication (too much, too less or not frequently enough). Read all about the shortcomings of manual lubrication in the article The pitfalls of manual lubrication.
- Automatic lubrication
An automatic lubrication system is one that provides your equipment with the right amount of lubricant at the right time and in the right place – usually while the machine is in operation. It replaces a conventional lubrication system and results in extended equipment life, reduced wear and smaller maintenance bills. Discover all the advantages of automatic lubrication in the article 7 significant advantages of automatic lubrication.
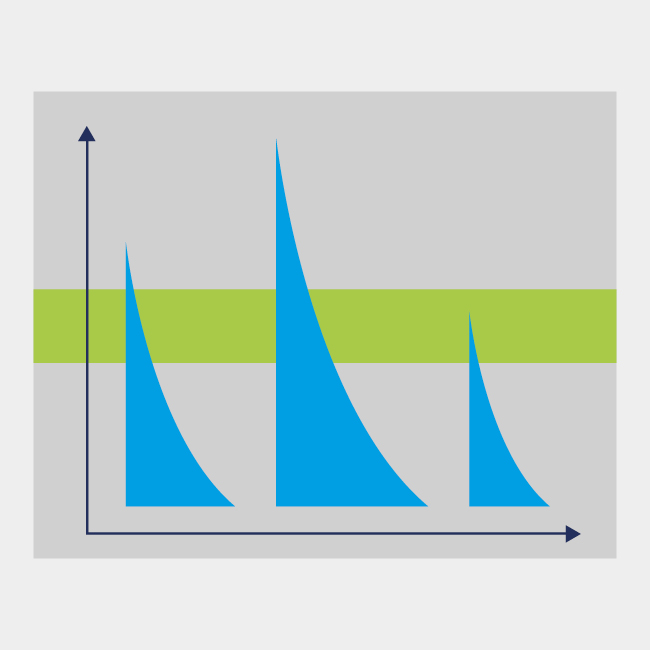
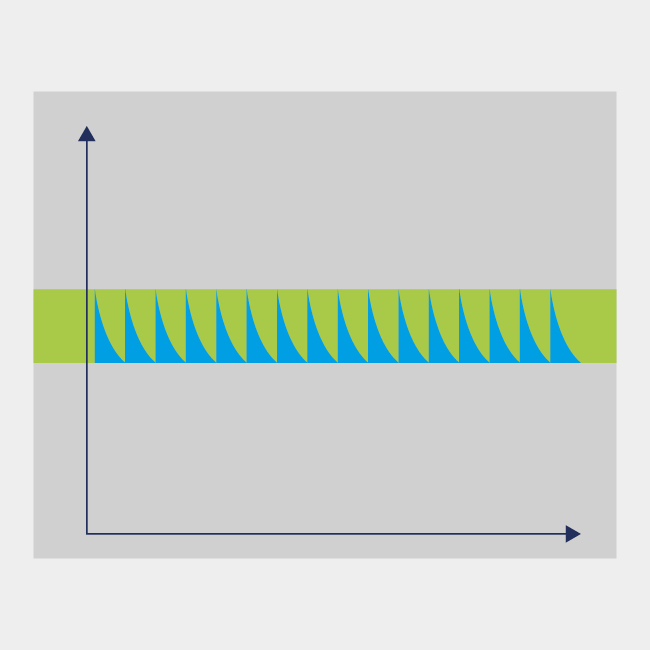
Manual vs automatic
Avoiding under and over-lubrication
“The effects of under-lubrication are well-known: increased component wear, premature failure, higher energy usage, increased operating and maintenance costs,” says Charles Hartl, Global Product Marketing Manager Lubrication Equipment Division at Graco. “But the effects of over-lubrication can be just as harmful. It wastes lubricant, can lead to excess heat build-up, puts stress on lube points and increases downtime. The solution is obvious: optimal lubrication.”
Why is automatic lubrication necessary?
Manual lubrication typically produces inconsistent lubrication. The uneven lubrication cycle leads to wasted lubricant, allows contaminants to enter the bearing, producing premature wear and impacting bearing life significantly.
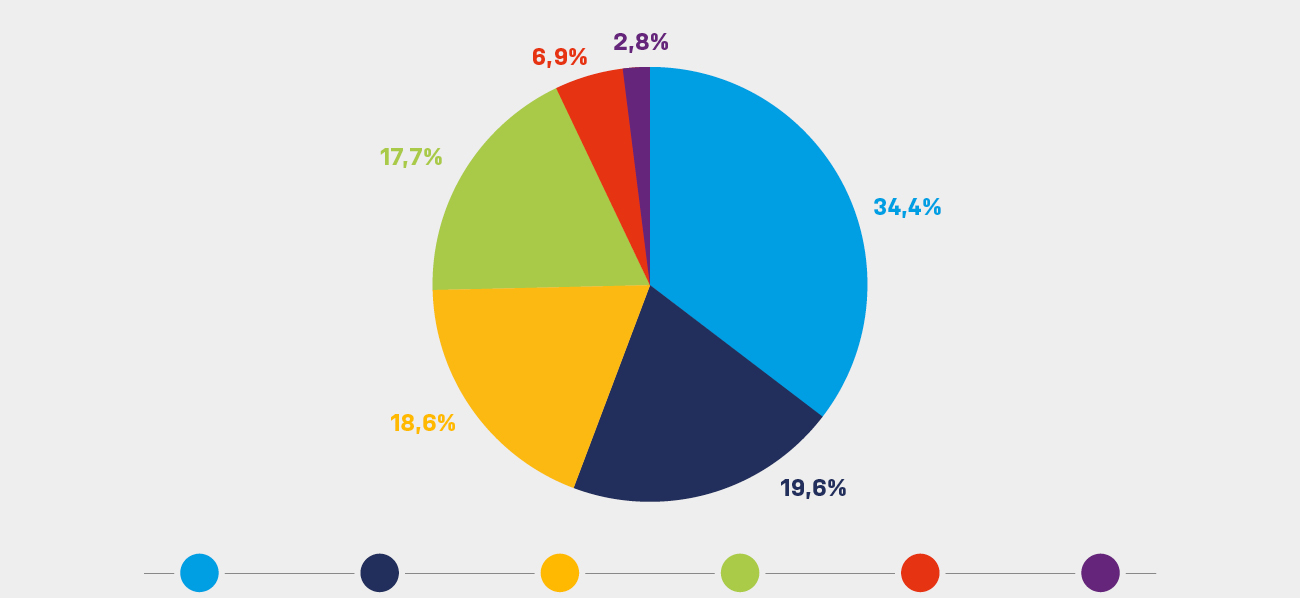
Why bearings fail
And that’s exactly where automatic lubrication comes in. It provides smaller amounts of lubricant at more frequent intervals, avoiding both over- and under-lubrication.
Automatic consistent lubrication extends bearing life and prevents unplanned downtime. Small, frequent amounts of lubricant while the bearing is in motion will increase the bearing life.
Automatic lubrication systems for all industries
Graco’s automatic lubrication systems can be found in several industries, such as:
- Marine
- Food
- Mining
- Construction