Tetra Pak chooses SaniForce to transfer tomato paste efficiently and profitably
When sanitary system integrator Tetra Pak approached a local Graco distributor in Jeddah, Saudi Arabia for a cost effective solution to transfer tomato paste from Goodpak crates into mixing kettles, they proposed Graco’s new Bin Evacuation System (BES) as a solution.
The traditional method and system used for this type of application proved costly, unhygienic and cumbersome. The end-user, SADAFCO (Saudia Dairy and Foodstuff Company) had limited factory floor space for such a traditional unloading system. The system required for the bag of tomato paste to be manually unloaded onto a conveyor and then squeezed out via rollers onto a conveyor, which then transports the paste into the kettles.
Together with Graco, the local distributor and Tetra Pak presented and proposed the Graco SaniForce BES to SADAFCO. The customer and integrator immediately liked not just the systems affordability, but also its footprint size, ease of operation and more importantly the clean, fast methods of transferring the paste directly from the Goodpak supply bins into their mixing kettles. SADAFCO’s Production Manager, Mr Ivo Gojanovic found the stated features and benefits of the SaniForce BES met his requirements. In particular, Graco’s claims that the BES can evacuate tomato paste with a viscosity of 190,000 centipoises at flow rates of 1,135 litres per minute.
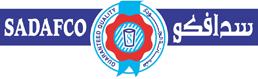
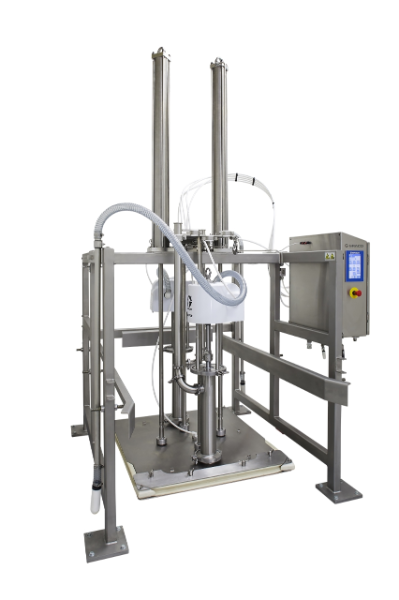
Flexible system suitable use for all bin sizes
Graco’s engineers in Minneapolis faced a bit of a challenge halfway through the production phases of the BES, when SADAFCO switched from their current tomato paste supplier to another. The new supplier used a different size Goodpak bin to those measured during the initial survey. Thankfully, another feature of the BES is the inflatable wiper seals. This means that the seals on the follower plate can be inflated or deflated to accommodate the new bin size. Engineering were satisfied that this would not pose an issue and continued with the production of the system. During the operation of the system, it also became apparent that the inflatable wiper seals increased the unit’s efficiency in terms of changing the bins quickly.
Successful installation
The supplied SaniForce BES system comprised of two SaniForce 3,150 air-operated double diaphragm pumps mounted on a follower plate. The system was controlled manually but does have an option to incorporate the electronic Micrologic controls.
The BES was integrated into the existing production line, mounted near a roller conveyor which is used to transport the bins to and from the BES. The BES is then plumbed into the mixing kettles
SANIFORCE BIN EVACUATION SYSTEM IN USE
The SaniForce BES is mounted over a loading conveyor system. After use, the system is cleaned out with the Graco HydraClean and it is ready for a new fresh bin.
The operator engages an air supply to the control box, which manually lifts the follower plate up in the air. The unique floating ram plate eliminates the need for the exact positioning of the bin under the ram place. The inflatable wiper seal increases the efficiency of the BES, and makes it easy quick change out of the bins.
The bin is then moved from the conveyor under the BES, where the operator then lowers the follower plate into the bin. The whole system is then plumbed into the main supply kettles, which feeds the factory.
Mr Gojanovic is very pleased with the service his company is enjoying from the Graco distributor. “They have gone the extra mile for us on countless occasions, and we are very pleased with their support”.
For more information about SaniForce Bin Evacuation System or solutions for the food industry, fill in the below form.