Case Study: Li-ion Battery Manufacturing
Foam Encapsulation Solution Fast-tracks New EV Battery Production
An EV battery manufacturer had to determine the best foam encapsulation process for a new cell module design. Quick collaboration with Graco put it into production by a critical deadline.
New Module Design Requires Cell Potting Solution
An electric vehicle (EV) battery manufacturer was facing a critical launch date for its new cylindrical cell module design. So that they could plan their production line, they needed a cell potting solution that met industry requirements to prevent thermal runaway and thermal propagation.
The foam encapsulation process had to be production ready. However, the design team and material supplier were having trouble determining the correct injection points and parameters needed to evenly dispense the correct amount of material into the module and prevent voids.
Encapsulation Process Challenges
Each cylindrical cell module design has unique features and requirements that can impact flow rates and dispense-injection points to dispense the correct amount of material into the module evenly and prevent voids.
The cylindrical cell battery module design was already established for production. To meet the deadline, success relied on fulfilling these EV battery foam encapsulation process requirements:
- Quality foam and fill: There was little space available for the flame retardant encapsulation foam to flow into and fill the battery module. The battery cells were closely packed together, causing additional flow restrictions.
- Optimal dispense: Dispensing had to be done from the top of the battery module with possible flexibility to inject from the side of the module.
- Rapid process time: Productivity was critical to the high volume battery operation.
Collaboration in Motion
The manufacturer’s battery design team and material supplier worked directly with Graco’s team of application engineers to develop a cell potting solution that met operational efficiency, product quality and repeatable material application requirements. They conducted these trials in the Graco application lab:
- Material testing: A thorough ratio and repeatability study defined optimal foam and equipment requirements.
- Equipment specification: The material testing, plus experience with similar trials, helped specify the best equipment for this encapsulation foam application.
- Application testing: The battery manufacturer supplied prototype models and modules used to assess and validate proposed process specifications.
The collaboration defined the flow rates, application techniques and dispense points needed for a production ready process in time for the launch deadline.
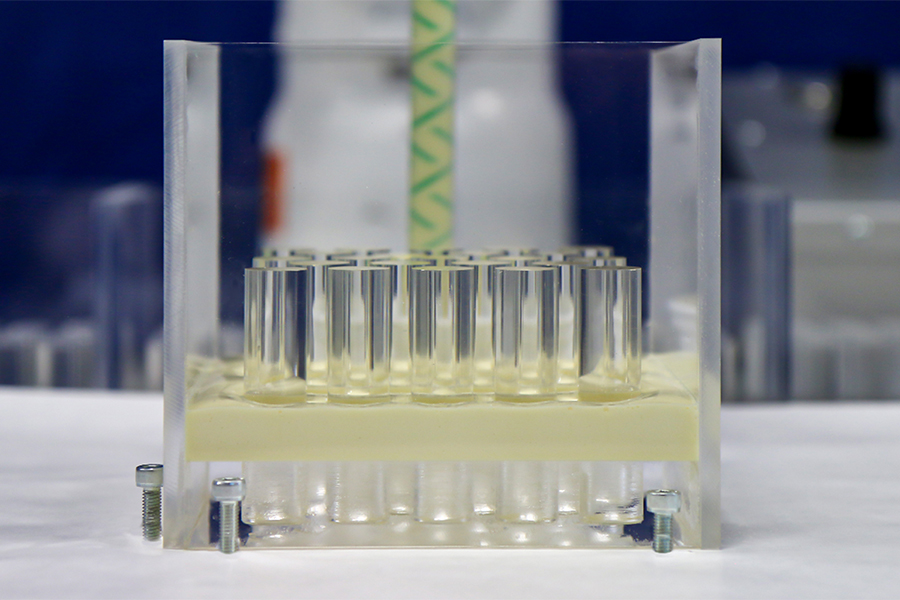
- Quality foam and fill: The Voltex Dynamic Mix Valve and Electric Fixed Ratio (EFR) Metering System provide thoroughly mixed form, even distribution throughout the module and shot repeatability.
- Optimised dispense: With the proper mixing parameters, flow rates and dispense-injection points, an accurate amount of material is evenly dispensed into each module.
- Rapid process time: The modelling and dispense trials helped optimised the motion pattern to reduce the required processing time.
Collaborate with Us
Innovation truly comes through collaboration with Graco expertise and material supplier partnerships. We strive to deliver custom solutions backed by our global support network.
Contact our team for help with your application.
Related Articles
Foam Encapsulation of Cylindrical Battery Cells
Learn about foam encapsulation and its role in the manufacturing of high-performance battery modules that remain safe under all failure conditions.
Thermal Management Benefits for EV Battery
Thermal management is critical for electric vehicle battery packs and requires durable dispensing equipment to withstand demanding application challenges.
Battery Pack Seal – EV Battery
A quality seal is critical for the performance and longevity of EV batteries and for protecting integral components from water intrusion and other harsh environmental conditions.