4,645 Square Metres (50,000 Square Feet) of Self-Levelling Underlay in One Day
Placing a Big Box Floor in a Day: Self-Levelling Underlay Pumping is up to the Task
Introduction
The thought of completing 4,645 square metres (50,000 square feet) of self-levelling underlay (SLU) in a day may have once seemed far-fetched for most flooring contractors. Using traditional methods, the lofty task would require multiple crews and heavy synchronisation to clear the work area, coordinate batch placement for proper curing, maintain access and monitor quality. With modern SLU pumping equipment, a single five-person crew can readily cover projects of this size and address many of the coordination headaches.
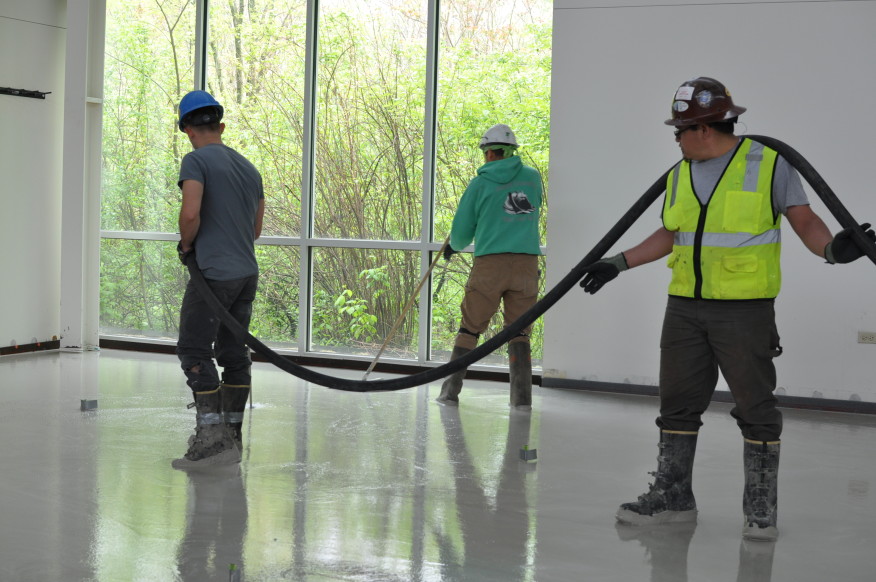
Preparation is Key
As with most construction operations, proper preparation is necessary to clear the way for high-production SLU pumping. Crews should first check the floor for areas of potential leakage. Cracks should be filled with spray foam, sealer or other patching materials.
The area must then be cleaned, so that it is dust-free. A combination of broom sweeping and vacuuming can be used to prevent dust from impacting the bond between the existing and newly poured surface. Once the area is clean, primer can be applied. Because the primer helps form a bond between the existing substrate and the newly poured SLU, primer application should be limited to the area of SLU to be placed that day. Primer may be ineffective for SLU placed on subsequent days.
With the area primed, the pumping equipment can be prepared for use. With units such as the Graco MP40, the water flow rate is set according to manufacturer’s directions, then dry material is added to the hopper and mixed with the water in the mixing section. With the water flow rate set, the equipment can be run all day long, producing consistent mixtures and placement. SLU mixtures can be pumped up to distances of 91 metres (300 feet) and heights of 18 metres (60 feet). Some form of damming material should be kept handy in case work is suspended unexpectedly. Loss of power, water, or other unplanned events could require work limits to be changed.
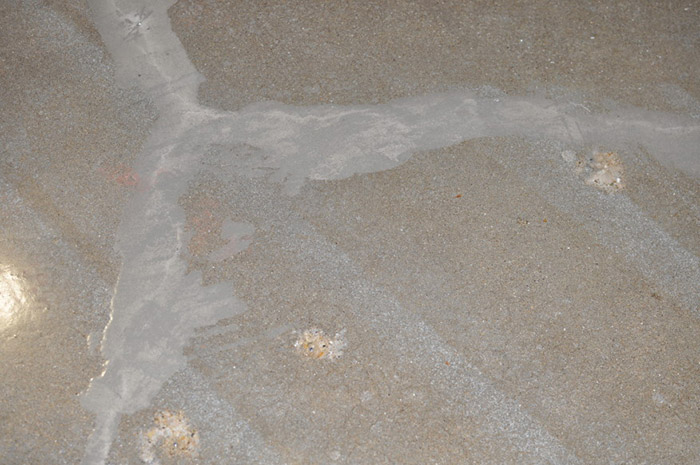
Cracks in the underlying concrete matrix should be filled with spray foam or other patching materials prior to placement of the SLU.
Start Pumping
With preparation complete, SLU pumping and placement can begin. Placement typically starts at the farthest point from the pump and proceeds back towards the pump, following a zig-zag pattern across the narrowest dimension. This enables workers to place SLU in widths of just a few centimetres at a time, or several metres at a time, while maintaining a “wet edge” and more continuity in the SLU layer.
To complete a large project with a six-person crew, each person has a specific job to keep the production running efficiently. Two people are needed to break dry material bags into the hopper in order to achieve up to 200 bags of material per hour. Because breaking bags is such a labour-intensive job, it’s important to rotate the crew around in order to keep personnel fresh.
Applying the mixed material are the remaining four crew members – one operating the nozzle and the pattern of the pour, one person managing the hose so it is not in the path of the pour and the other two people smoothing material using gauge rakes.
As work proceeds, crew members need to add dry material as needed, manage the hose as work progresses toward the pump and continually place and smooth the material. A continuous wet edge of material should be maintained across the entire placement area.
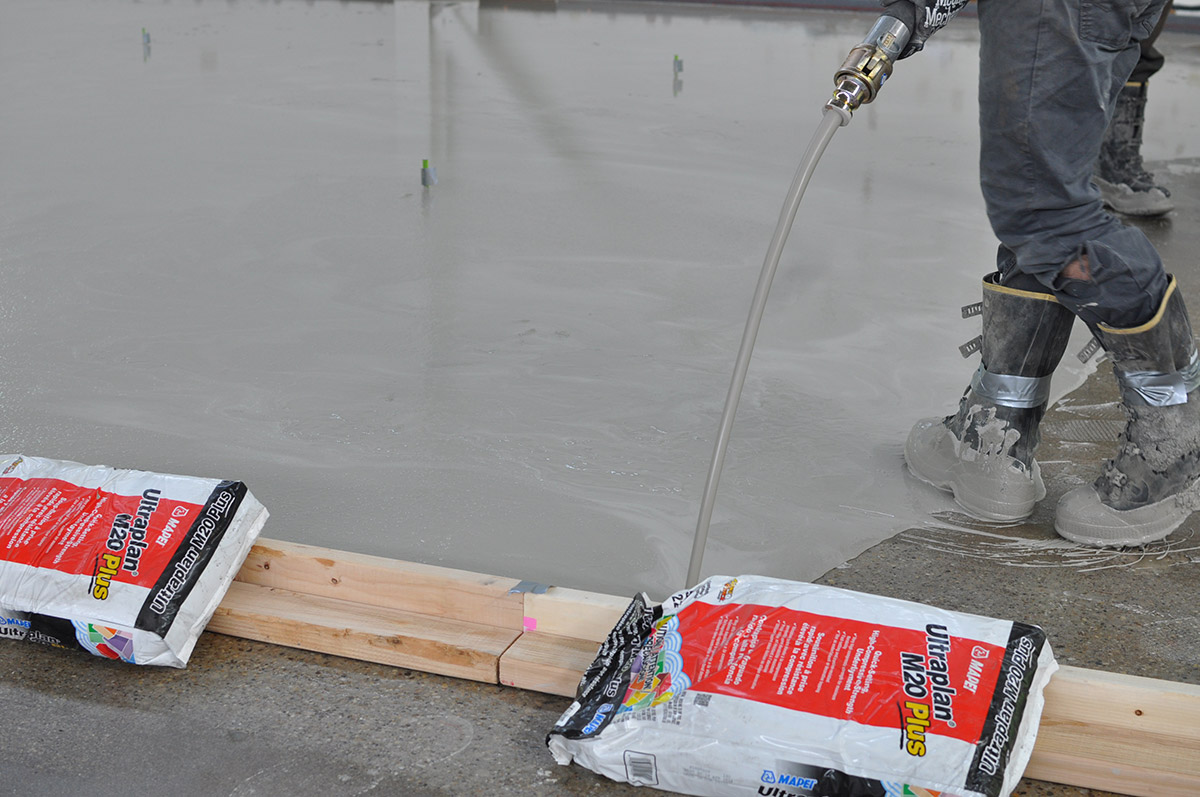
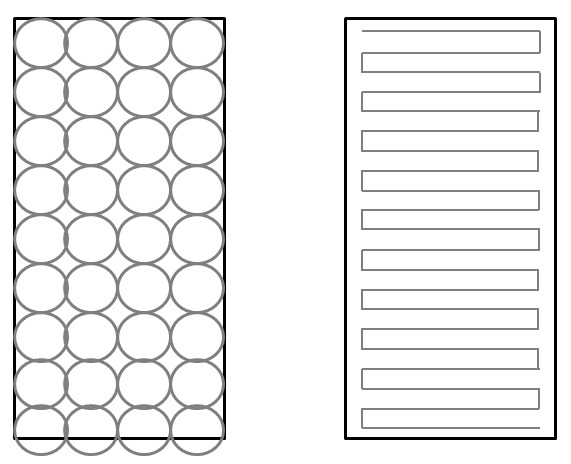
Conclusion
The SLU pumping approach can expand the horizons of traditional SLU contractors. In addition to simplifying scheduling, pumping can enable crews to tackle larger projects and complete projects faster, leading to greater profits. Assuming a $0.50 profit per square foot on a 4,645 square metre (50,000 square foot) SLU with 0.64 cm (1/4-inch)-thick flooring substrate, an SLU contractor could conceivably pay for a pump in one day. With improved quality and consistency as benefits, a switch to pumping may be a wise choice for SLU contractors.
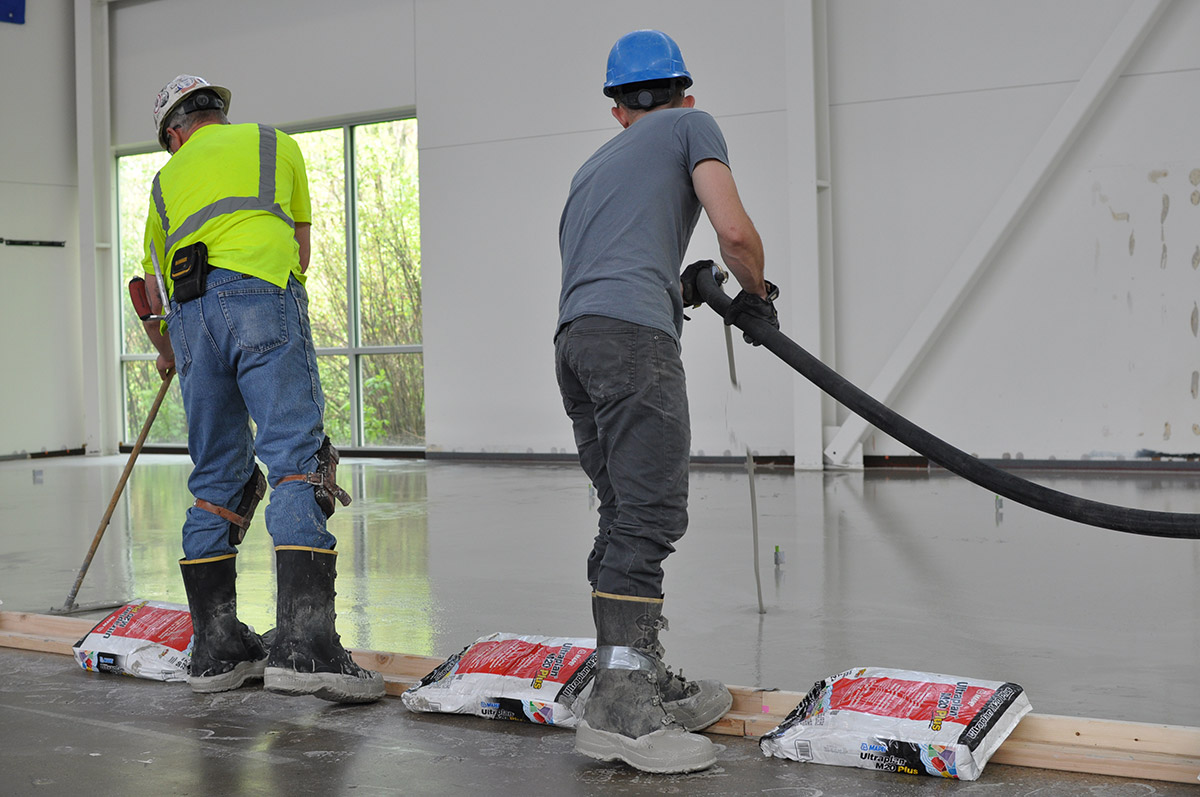
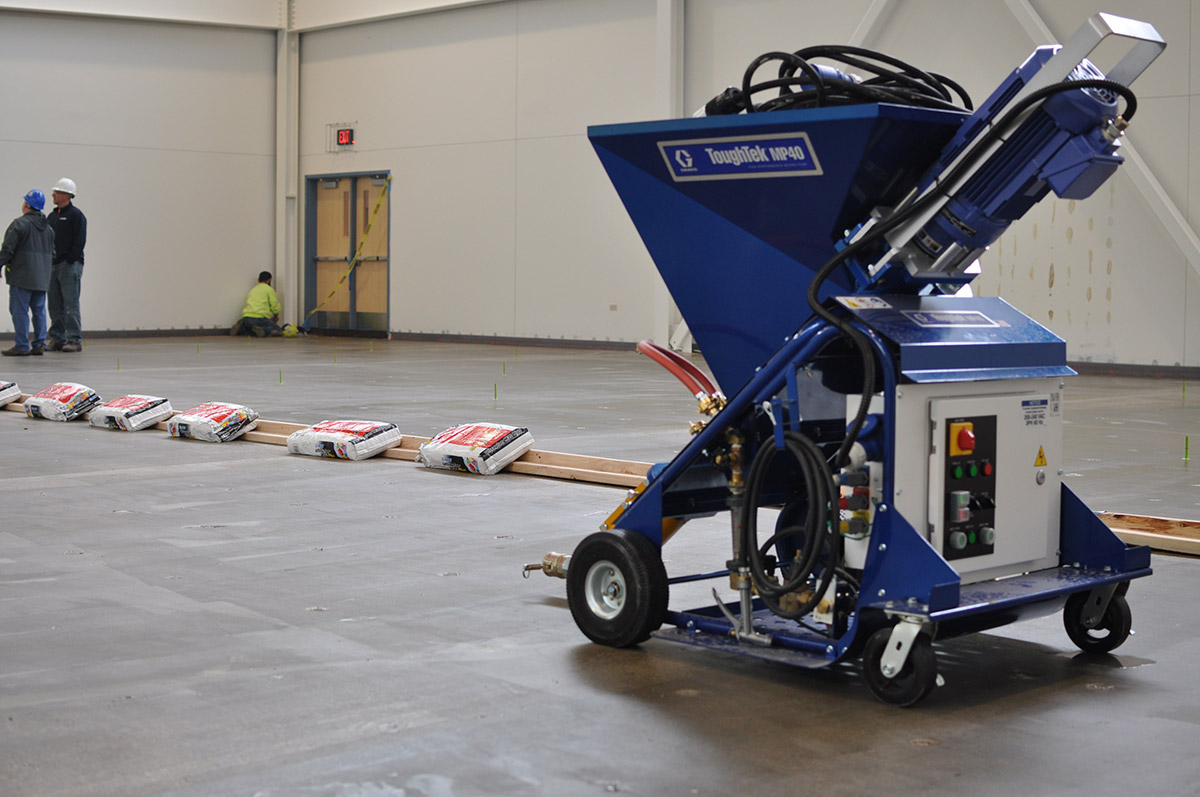
Related articles
Spraying Techniques for Electrostatic Airless Disinfectant Sprayers
Learn more about the power of high-pressure electrostatic airless sprayers and maximising efficiencies when spraying disinfectants.
Spraying Techniques for Airless Disinfectant Sprayers
Using a dedicated airless disinfectant sprayer provides the fastest way to achieve consistent coverage of disinfectant materials across any surface being sprayed.
Spraying Techniques
Understanding and applying these basic spraying techniques will be the difference between a sloppy looking paint job and a professional one.